after four months, a new master of machinery has been revealed and the new bikerMetric techTips master contributor is mr. hugh owings. he has a shop in asheville. he drinks both great and ****** beer. he has a generous smile and a wife who reflects the same. they made both eric and i feel most welcome when we visited this summer and invited us to stay with them any time. suckers. *** bless their hearts.
his articles will be posted with the oldest first. as you read, you’ll learn more about your bike, instead of having to do it in reverse.
if you like this first article, please comment below and share it with all you know. these are (mostly) hugh’s words. these are his photos. this is his knowledge. welcome to his pink drop cloth:
Well gang, it’s time to look into the soul of your XS650. No, I’m not talking about your Sportster tank or that TC Bros tail and apes, those are merely makeup on what might be a super hot chick under that emo mess, but, without getting down and dirty with your engine, looking cool ain’t doing you much good. Let’s face it, the newest XS650 on the road is 27 years old now, and if you got an early model XS, you are pushing 40 years. I know Jappers have that “live forever with no maintenance” reputation, but when you are dealing with bikes that have been dragged out of sheds, swamps, barns and fields, you are bound to have some problems. Just like old Triumphs, all the power and reliability in an XS650 engine starts with the crank, and also like Triumphs, the XS650 crank and bottom end are usually the most neglected part of a build. I’m not going to show you how to tear down your engine, buy a Clymers manual for that because you are building a bike for *** sakes, and it can’t hurt to maybe flip through a few pages instead of hitting Google every time you need something.
Now that we’ve got that out of the way, how can you tell if your crank is any good? Well, I’ve got a few simple steps to check over, and I’m going to show you the process of re-phasing the XS650 crankshaft while we’re at it. For some companion information on re-phasing, visit hughshandbuilt.blogspot.com/2011/01/re-phased-goodness.html.
First, get a decently clean work surface and toss down a few shop rags if you have to. For most of you, after you tear down your crankshaft it will look something like this:
Now you’ll want to remove the charging rotor if you haven’t already. Take a 17mm socket and if you are lucky enough to have an impact gun, use it. If not, then you are probably already well versed in curse words, so no need to go into all that either. Get something to keep all your parts in because it’s going to get busy and you don’t want to lose anything.
Now you will need a special remover only if you want to save the charging rotor from further damage. If your bike is like 80% of the XS machines out there, this thing is already crapped out and is going to be another nightmare if you keep it. Not surprisingly, I have a fix for that at hughshandbuilt.blogspot.com/p/xs650-permanent-magnet-alternator.html. If you aren’t interested in buying any special tools, and don’t plan to keep the crappy stock charging system, a standard puller from the local Vatozone will work fine. Either way, get that sucker off of there.
See all that **** that came out of the stator? Thats a good sign it would have left you sitting on the side of the road, far far away from home (or anyone who cares to come get you, trust me…)
Okay, now that you’ve gotten that out of the way, let’s actually get to the crank itself. Find a cheap ruler, something with metric measurements – that’s the superior system of measurement by the way – and position the rods over the ruler like so:
Wiggle the small end of the rod side to side over the ruler. You should have less than 2mm of movement. If you are right at 2mm, you are probably okay for now, but keep on reading….
Inspect the small end of the rod closely and get a flashlight if you need to. You are looking to make sure the entire ID (inner diameter) of the rod end is still coated in a copper color. If you see a lot of silver, you are at the end of your rod’s life span. If there is a small amount (less than 10%) of the total area showing silver, you are in that gray area of reuse. If you see any scoring or gouges, it’s time for new rods. Most simply put, if in doubt, get new rods.
At this point you are probably ****** off that your wallet is gonna be a bit lighter, or you are feeling pretty good about your old rods. The rods pictured here were good enough to reuse at this point. Either way, you aren’t done yet. Take a 22mm socket and remove the nut from the drive end of the crank. Pull all the parts off of that end and inspect them all for unusual wear such as cracks and pits. 99% of the time these are in good shape, but I have seen several engines that must have sat in a swamp and had that motor oil replaced with rusty water, so take your time and inspect everything carefully.
Go ahead and remove the bearings from the ends of the crank. You’ll need a set of snap-ring pliers. I recommend that since you are rebuilding the XS650 engine, do yourself a favor and do not get a set with changeable tips because they suck. You can use a clamshell bearing puller, available at most auto parts stores, or a variety of chisels to remove the bearings. If you are limited to chisels, you can wedge the chisel between the bearing and the flywheels to remove the bearings. Don’t worry, these bearings are pretty tough. Once they are off, check them closely for pits, scoring, and smooth operation. Take your time as this is the heart of your engine and once we are done, this crank will be capable of very high RPM’s if you do this right.
Now things get interesting. A lot of people would have stopped at checking the rods, but hang in there and do it right the first time. You are going to split the #2 and #3 flywheels from each other. You can use a press and wedge blocks, or take it to a shop and have it done. Any competent motorcycle repair shop should be able to do this. Don’t bother taking it to the Harley dealer your cousin works at, they haven’t quite caught on that the “V” in V-Twin stands for “Vertical.” That’s right, we’re starting a revolution and your little 650cc parallel twin is going to smoke a 96 inch vee cube like the Lords of Loud smoke crack through a crunched Keystone Light can.
Go ahead and pull the cam drive gear and all the bearings and shims.
At this point you will either have a 20T press at your disposal or you’ll head over to the local repair shop to have them do this for you. If your engine has been sitting for a good long while, spray some WD-40 or something similar on the rod bearings to get the pins lubed. You want them to slide out easily and not bind. Press out the rod pins.
Once you have the pins out, inspect them closely for any wear or pitting. You know the drill at this point. You’ll also have to inspect the large end of the rods and the roller bearings for any damage. Again, if in doubt, get new pins.
You can see some gouges in the pins which were caused by the thrust washers binding and cutting into the rod pins. This is fairly common, but these are bad enough and will be replaced. You can see in this photo the gouges circled in blue marker:
Also notice the pin in the top of the picture was galled a bit while being removed. You’ll want to replace them at this point. Luckily, you can get them for a reasonable price from mikesxs.net, along with rods if needed.
At this point, you’ve earned a good break. Take time to wrangle up a good beverage and/or grab a snack. You should have a pile of parts that look something like this:
We’ve covered a lot of parts that could cause a potential engine failure if not checked. It sucks to lose an entire engine due to a $40 bearing going bad. So pay attention.
I’m gonna show you a little bit of what I do to re-phase a crankshaft. I build about two or three of these cranks a week, and when going for high horsepower or even if just planning a Big Bore, you should build a proper crank, or have someone do it for you. If you are going with a basic rebuild with a stock bore, skip all the welding. I’ve seen plenty of stock cranks come through my shop that were very close to failing when pushed hard. Even with a basic 750 big bore kit, the crank takes a beating and will start to separate and claw its way out through the cases looking for freedom. If you’ve been having charging system problems and the rotor is crashing into the alternator housing, it’s probably a crank problem. Trent shot a short video describing that in more detail here on his YouTube channel.
When I build an engine, I expect it to handle some major abuse. Any reputable performance engine builder will weld the crank pins but I take it a step further and weld the #2 and #3 flywheel together as well. Let’s start reassembly:
Clean everything with some denatured alcohol or Acetone. You don’t want any oil on these parts or you’ll have a contaminated weld and life will suck. The bad kind of suck.
With the new rod pins pressed into the flywheels, I TIG weld them in. You cannot weld these pins properly with the bearings in place, or if you haven’t removed all the oils from the press joint. This is the reason I completely disassemble a crank and don’t just half *** it. Use your whole ***, folks.
Make sure you assemble the bearings, shims and cam gear in the proper location because once you press this together and weld it, you are committed and there is no turning back. If you are re-phasing the crank, you’ll want to relocate the cam drive gear and index the splines properly. If you’re returning to the stock configuration, then keep the two rod pins in the same plane. Press the #2 and #3 flywheels together very carefully, making sure not to bind them or bend them at all. The crank pictured in this article is being re-phased for a customer, so it will look different from stock, but all the principals are the same from here on out.
Now measure the runout on the flywheels. You should have zero runout if you’ve done this properly. If not, you may need to disassemble the flywheels and look for a bent main shaft. You’ll need a dial indicator for this and a magnetic stand. For this you can use the bottom case as a “jig.”
If everything measures properly, you can weld the splines of the #2 flywheel to the #3 flywheel. This will keep the crank from separating under high load or at high RPM.
Reassemble the thrust washers, rods and rod bearings, and press on the outer flywheels. As mentioned above, you’ll want to get the runout of the outer flywheels. Any runout at all will cause a violent vibration and can lead to cracked cases, leaky seals, and generally **** you off. Then the police come and now you’re begging friends and bail bondsmen to save your sorry ***. If you’re trying this for the first time, be prepared for it to take a few days. The very first crank I built myself took almost two weeks to complete. I thought I was going to lose my mind, and nearly gave up on my entire project. Be patient or have a professional handle the job.
Once the runout is completely dialed in, I weld the outside flywheels to the rod pins.
This crankshaft will handle just about anything you can throw at it now, and being re-phased, it will reach much higher RPM and vibrate much less. Save your genitals for banging doggy style. For those of you riding a bone stock bike, you will never understand how badly these engines vibrate in stock configuration because you are riding on about 6″ of super sweet foam. But for those of us riding on a rigid frame with about half-an-inch of seat padding, we know what it’s like to be riding along with the engine vibrating your nuts and guts out. *** forbid if you fart with the engine above 4500 RPM, you’ll think for sure you just crapped your trousers. Re-phasing gets rid of all that, but I’ll leave it to your own research to decide if it’s a mod for you.
Finally, don’t be fooled into cutting corners, whether you do it yourself or are paying to have it done; do it right the first time. You’ll be glad you did and you’ll never worry about the bottom end again.
I sign and date all my cranks – get the real deal! Maybe in 2068 everyone will be paying ridiculous amounts for a real “Hugh’s HandBuilt” crankshaft for their “period correct” XS650. Until then I think my services are quite modestly priced. As always, I’m glad to help out with your tech questions via email.
+ + +
there you go, mofos. hugh’s next techTip is already written. look for it in the next week or two. until then, remember:
All right folks, last month we left off with a freshly built re-phased XS650 crankshaft. Well, that crank has long since been shipped to the owner where it’s hopefully tearing up the streets and being a menace to the vintage bike enthusiast crowd.
That’s not to say I don’t always have something going on here at Hugh’s HandBuilt to keep your mind alive and help convince you to get your hands dirty. Today I have an engine that is a very special build. It is from a very early XS1, and we are updating it with re-phased guts, 447 rods, a 750cc big bore kit, updated cam chain system, late model transmission, and fifth gear overdrive, along with a few other little tricks to bring it up to par. Some of the differences in this particular set of cases will be noticeable to the naked eye right away.
The most noticeable difference is there is no location for an electric starter. Some of the stud locations are very different and there are more bosses and cast-in webbing for extra strength. Other interesting differences? There are more machined oil passages for the transmission and the cases suggest 3000cc of oil, while later models suggest much less. Once I had these cases stripped, I noticed a funky yellow stain on the alloy. There is a rumor that this engine might have been used in the Flat Track racing circuit and given the amount of repair these cases required, I believe it.
For those of you with a more common XS650 engine, don’t worry, everything you read here applies to your build!
Now you have a really clean and nice set of cases ready for that crank you built, right? If not, don’t read the rest of this article because you can’t build a great engine with sub-par effort. Nasty engine cases are a sure fire sign of a poorly built engine. Take pride in your work. Now that we have that out of the way and you’ve got a set of perfectly cleaned cases, you should have something like the photo above, ready to go.
The owner of this engine wanted his cases coated in high-temp low gloss black. If you decide to paint your cases, make sure to tape off all sealing surfaces prior to painting. If you think a “rattlecan rebuild” is the ticket, forget about it. Painted gaskets, bolts, and grime are a quick giveaway to a “rattlecan rebuild” and you aren’t fooling anybody. Take the time to clean all the threads on your engine before installing the first component. There is a good chance your case studs look a lot like this:
Rusty and corroded threads must be cleaned up before you can try to properly torque any hardware. If you are like me and live in an area where specialty tools are hard to find, you might make your own. I don’t like waiting on special tools to come in the mail so I make what I need. Today we have a cool little trick.
I need to clean the stud threads on these cases. They have several years of crud, crust, and paint on them. I will chase them with an M8 1.25 die.
Doing this job with a standard die holder sucks and takes an incredible amount of time. Instead, grab a socket that your die just barely fits into. Go to your drill press and drill a hole suitable for a small set screw. I used a 3.3mm drill and tapped 4mm x .70 threads since I keep that size set screw in stock for my fork lowering kits. Use what you have, it’s a tool after all, and no, this won’t hurt your socket but I would choose an inexpensive brand socket before drilling into my Snap-On goodies.
Keep enough room inside the socket for the longer threads on the studs by locating your die near the end of the socket like this:
I’ll assume that since you’ve made it this far, you’ve decided to do things properly. Good for you, the world needs more properly built bikes and there is nothing that feeds the HD crowd with higher-octane fuel for the hate fire than a broken down *** bike. Since we are cleaning the threads, get some oil to keep the die running smoothly over the threads. Remember, we aren’t cutting new threads, just cleaning up the old ones. I do a lot of machining and tapping so I usually have some tapping fluid around. If you don’t have any, a little bit of Marvel Mystery Oil and automatic transmission fluid works wonders as well. If you don’t know what Marvel Mystery Oil is, fart loudly at Christmas dinner with your parents. It’s what they get for not teaching you very important things in life.
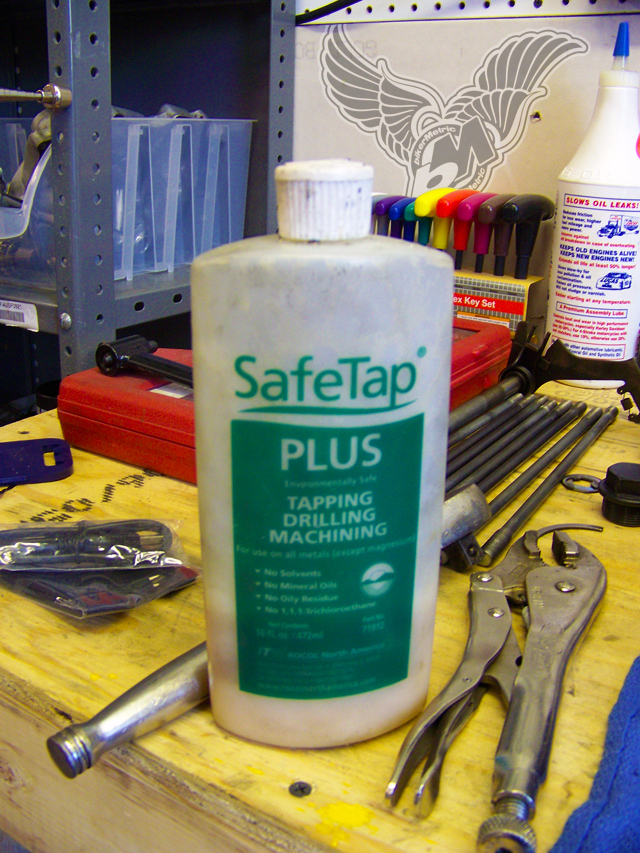
Always start your taps and dies by hand. Not doing so will surely wreck your threads and your neighbors will likely learn the extent of your five or six-word verbal communication skills with inanimate objects. Not that it won’t happen at some point, because I’ve been there plenty of times, but don’t be in a hurry. It saves time and energy to do things right at the outset, and then you won’t be cursing a defenseless engine and throwing tools into the darkest corners of the shop to never be found again. Find your engine building mojo and have fun with this stuff.
Once you have your die started by hand, feel free to use a socket wrench to speed up the process. Once you are done chasing the threads on the studs, clean all the oil off with some brake cleaner or such. You’ll want these studs perfectly clean for the Loctite you’ll be using later.
Now that you’ve got that over with, you’ll want to get a good M6 x 1.00 tap. For this kind of job, I prefer a four-flute bottom tap. You’re gonna be at this for a while, so grab a cold one and remember, don’t rush.
There are a few other threaded holes in the cases you’ll want to clean out, but by now you’ve got the idea and I don’t need to guide you through all that. Just make sure all your threads are clean and good to go. Recheck everything at this point to be sure.
Now onto the good stuff….
This transmission is getting a nice little upgrade. A fifth gear overdrive is available from Mike’s XS for later model transmissions. We are swapping the transmission from an 1980 model into this engine and are good to go. If you are not changing the fifth gear on your transmission, keep reading and we’ll get to installing the transmission just like a stock one.
Pull the bearing and shims off of the transmission input shaft. We are removing the 2nd gear from the end of the shaft. You’ll need to remove a snap-ring while you are at it.
Slip off the stock fifth gear. This is the only part getting changed to upgrade your transmission.
Keep track of the various shims and snap-rings. They will reinstall in order from top to bottom from this picture:
This your new fifth gear. It looks similar to the stock gear but with a different tooth count. I’ve run one of these gears for thousands of miles, so have no worries about their quality. There is no noise difference, and lowering your cruising RPM is nice for many reasons. Or, if you are a speed junkie like me, you can run some deep gearing for triple-digit speeds!
Reinstall all the parts.
Take the top engine case and lay it down on your workbench. I remove the engine studs on all my builds, so this step will be a bit difficult if you have not done so. You can get away with shimming the case up off the studs but having the top case upside down is a must for the proper installation of the transmission and crankshaft.
Align your transmission gears with the shift forks and drop them in. Make sure to line up the cir-clips into the grooves on the cases. I have pointed out the clips here with my Sharpie:
Once you have installed the transmission, run it through all the gears and make sure you’re happy with it. Now you are ready to start setting the seals in place. I use only genuine Yamaha seals on my builds and get them locally through an independent moto shop. They cost the same as the non-OEM **** you can get from Mike’s XS. Support your local shops. They need you and you will need them at some point. It’s always good to be a familiar face in your local motorcycle shop [editors note: from personal experience i know hugh is right].
Now this particular seal is a total pain the *** if you choose to install it after you have the cases together. They constantly leak and get mangled to death if you try to install one without the cases split. Save yourself some time and install the seals now while your cases are apart.
Early Yamaha XS650 engines came with a one-piece clutch rod. If you don’t have one, go get one. They are available from popular XS650 suppliers. They have smoother clutch action, less leaks which makes them $16 well spent! This one is a bit beat up, and is being used only as an example for this techTips. A new one is on the way.
This is the most critical part of your bottom end build. The locating pins are crucial in making sure your crank gets the oiling it needs to stay alive. I’ve indicated the pin here with a yellow paint pen.
On this bearing race, you can see two lines. These will line up with the case mounting surfaces. I went ahead and marked them yellow so I could see them while I was working. Your crank will have three of these bearings with two in the middle of the crank. Lining these bearings up is critical. As always, take your time and make sure they fit properly.
The large main bearing on the crankshaft will sometimes have marks that line up with the cases, but not always. Don’t be in a hurry to locate them, if they exist, and put some defining marks on the bearing for reference. If you have to, pull the bearing off the crank and install it by itself in the cases and make your marks. It’s worth taking the time. Trust me on this one. I see more dead cranks and burned up engines from folks not doing these steps properly.
Slowly line up all four bearings in their journals on the engine case. Don’t force anything to fit. When they are in the right position, the crank will drop into place.
Leaving a little bit of room on the edge of your workbench for the rod ends to dangle will keep the crank from wanting to pop up while getting the bearings aligned.
Spin the crank a few times to make sure all the bearings are seated. Double check all your marks. Once you have the crank bearings fully seated, take a break. Eat a sandwich. Smoke your cancer stick. Drink a beer.
After a little breather, get some lube and put it on the transmission gears as well as on the big end of the rods. I use Lucas, because it won’t run all over the place while I’m building the engine.
We are now ready to put the cases together. I like to use Hondabond on my Yamaha engines. I’m weird like that. Make sure you use something similar but do not use a thick gasket sealer.
Here is a great tip; make sure you put Hondabond on all of the case mating surfaces. These locations typically cause leaks from the bottom of the engine as oil follows the studs. By sealing all the stud locations, you won’t need those pesky copper sealing washers. More on that in a bit…
Apply some Hondabond to all of the machined mating surfaces of the crankcases. A little bit goes a long way and I usually blend it out with my finger as I go. The nice thing about these sealers is that you don’t have to worry about “squeeze out” if you use too much. It will not break loose and cause a ruckus in your engine like normal sealers.
As you may see below, I like to add an extra bit of sealer around the bearing edges and seal edges to be sure I won’t get any oil leaks. Once you have all your sealer on, you want to move fairly quickly with the next few steps, so put the beer down!
Since I was working alone on this project, it was tough to get a picture of putting the two case halves together. It’s not rocket science. Simply line up the studs, make sure the locating dowels are in place and drop the bottom case onto the top case. Do not force the cases together! If they don’t easily fit, you have a problem.
I like to use all new hardware for these builds. Since we put sealer on all the stud locations, we no longer need to worry about the copper sealing washers under some of these nuts, as I hinted above, and you won’t be losing hardware as others do on a stock engine. Nice touches like this create a long-running, non-leaky engine.
Make sure all of the studs get new stainless washers and nuts. I install the washers and then add a drop of Blue Loctite or Loctite Threadlocker to the studs.
Torque all the nuts down to the specific torque as described in your manual and yes, you need a manual, so get one. Don’t forget that hidden nut and stud behind the clutch basket or the ones behind the final drive sprocket. They are often overlooked.
Flip the engine over and install new bolts in the remaining locations. If you are using stainless hardware, always put a dab of Anti-Seize on the threads. Stainless and aluminum do not like to dry hump, so lube it up!
Torque those suckers to specs and you are done!
Next month we will look at a few other cool upgrades you can do to the bottom end of your XS650 engine. Until then, stay in the shop and get creative!
+ + +
Thanks, Hugh. Like last time, this was informative and well-documented with more photos than a stick could shake itself at. My stick is a stump after this one. Now how am I going to keep those punk kids off my lawn?
Remember folks, if you get stumped (ha, that was funny), need tech advice, or want to buy lots of Hugh’s world famous parts and services, visit his blog, check out his website, or simply email hughshandbuilt at gmail.com.
Peace out and thanks for stopping by.
______________________________
Here is our latest installment of techTips by Alex Chopperbuilder that he has called:
First though, let’s look at a couple of things to get us in the mood and the right frame of mind (Frame of mind! Get it? You know sometimes I make myself laugh. No? Please yourself!). Moving on….
What is a frame ? Well technically there a few different definitions around and they all tend to be filled with technobabble that seems to be designed to keep people from finding anything out about them and to make the people that write the definitions look clever. On my planet we have a word for this, it’s “bollocks.” A frame is nothing more than a carrying apparatus to hold all the parts together that make the motorcycle do what it does; i.e., be ridden by a person and to keep the wheels in a correct relationship to each other at all times. Let’s call that Frame Fact #1.
What else is there? Well, not much once Frame Fact #1 has been established there really are only two other considerations to be taken into account. The first is “how it looks,” and the second is “how it handles.” Both of these attributes are subjective and both are a matter of personal taste. In the world of custom bikes, very often extremely radical personal taste is taken into account as well.
Therefore we need to decide what type of frame we want to build. This is dictated by the type of bike we are after: chopper/bobber/café racer/tracker…
What we are going to do for these articles is to go through the steps and procedures necessary to build a rigid chopper frame. There are a couple of reasons we’ll discuss rigids for this; it’s arguably the most simple of frames to write about building, and it’s a good frame to start with for a novice frame builder. For example, there is no need to take into account rear suspension set ups and geometry, and we also need to be talking in a pretty general way for this type of article and a rigid chopper frame fits the bill quite nicely, so let’s run with that. This is the beginning and the basics of frame building apply to all types of frames, so we’ll keep the complications to a minimum to start.
What do we need in our shops to attempt building a frame? We’ll make a couple of lists, (you knew I was going to say that) and we’ll start with the personal skills that will be useful/needed. Bare in mind that if you don’t have some or all of the skills I’m about to list that you either need a very fat wallet, or a buddy/buddies that you can coerce/bribe/blackmail into helping you out.
Skills (in no particular order of importance):
1. Basic metalwork skills
By this I mean the ability to use a hacksaw (and cut straight) and a file (and file flat). basic metalwork skills include the ability to use a drill press and a hand held drill and center punch accurately on the tube (I suggest you practice on that as it isn’t as easy as it looks). Lastly, you need the ability to use an angle grinder and the various discs available including wire brushes.
2. Welding skills
Go back to our Setting Up Your Home Garage articles below. TIG welding skills are outstanding and current state of the art in the bike building world. But MIG is perfectly good enough for frame building. PLEASE! IF YOU HAVE ANY DOUBTS WHATSOEVER ABOUT YOUR WELDING ABILITIES, GET HELP FROM SOMEONE EVEN IF IT MEANS TAKING A COURSE. And, no I won’t apologize for shoutin at ya’ll. Some things are too important to whisper.
![]() |
fishmouth tube notch |
You need to be at relatively proficient and at ease with the tools mentioned above. If you have metalwork experience but not much in tube work, a surprisingly common scenario, get hold of some cheapo scaffold or steel plumbing pipe and practice your techniques on it. Practice cutting it square and notching a fishmouth into it, practice drilling through squarely, both with the drill press and the hand held. Before you take a pen to paper or a finger to a keypad to order your steel tube to build your frame, practice, practice, practice on some cheap **** to get your confidence up, you’ll be glad you did. As in all things in your workshop, common sense must prevail.
That more or less covers what you need to know how to do yourself. Now for…
Equipment:
1. A frame jig
Previously mentioned in our Setting Up Your Home Garage articles. There are drawings and plans available for these all over the internet, some are gold some aren’t. It would take years to try and assess them all, so I have to leave that to you. Hopefully by now you’ll have sorted something out that suits your needs, and it’s sitting there in the shop awaiting some funny shaped tubing.
![]() |
home made frame jig |
2. Tube bender
This is the same deal as with the jig. Although technically you don’t actually need to own one (unlike the frame jig), as long as you have handy and available access to one, you’ll be fine. By handy I really mean in the same street, if not next door. Yeah. I know it’s unlikely, I’m just trying to cover all the bases and save you a few bucks. Friends with tools good.
3. Hand and power tools mentioned above
Get a good assortment of discs as well as drill bits.
4. Tube notcher
This is not essential because there are other ways of doing it, but if the budget will run to it, get a tube notcher. Joint Jigger is a good example, although there are a few good ones out there. I have to admit that when these first appeared I was skeptical to say the least, I dislike “gadgets” intensely and saw these as the same. Then a buddy of mine got one and I borrowed it to evaluate and was sold. They are a godsend and that humble pie tasted really good! Seriously, they are very useful and most importantly they are accurate (as long as you can read a tape measure). Oh and before I forget, check out this little beauty, a tube coping calculator. It’s a very useful little program for calculating and producing a template for any given angle of notch and tube size. I won’t bother explaining more, just download and have a play. You will need a printer to run off your templates, so click here for that.
5. Last but not least, SAFETY EQUIPMENT!
C’mon now people, you’re all grown-ups and I already mentioned common sense. Have an operable fire extinguisher or two handy, safety glasses, gloves, etc. This is all good, clean, dirty fun, but it sort of takes the shine off when you’re sitting in the emergency room having an eye taken out or a finger or two sewn back on.
Be careful and have fun while remembering this is a positive and creative pastime and we all want to enjoy the fruits of our labors, not to mention the labors themselves.
That more or less covers what we need as far as our skills and tools are concerned, but what about materials I hear you ask?
Looking at the basic chopper type frame we are going to be theoretically building it’s actually a pretty simple affair in reality. Regardless, there are a few obvious differences between the average rigid frame built to take an Ultima El Bruto and running gear and a Yamaha XS650 motor. The design fundamentally remains the same for both models, they will be different in length for sure, but that’s a pretty obvious difference. What isn’t so obvious is the frame tube size. In general the “industry standard” tube size used by most builders for big twin builds is 1.25” Dom or Seamless Tubing, in 10 and 12 gauge wall thickness.
Make no mistake, this is pretty serious structural tube. Especially when we look at what the factories are using on their frames. Harley uses 1″ and 7/8″ diameter on their big twin frames and most Japanese factories are using 7/8″ on their frames. The really big difference that none of us can see is that no manufacturer uses seamless tubing exclusively and the wall thicknesses of some of the factory frames tubes is downright scary to see. I’m not saying that the factory stuff is badly built. To be fair, we don’t hear of frame problems today with steel tubular frames, so they obviously work.
So why has the custom world ramped up on tube dimensions? There are a couple of reasons for this. Back in the day (1970’s) when Mr. Ness and chaps like him where building what have become known as Diggers (choppers were soooooo 1960’s, dude. Get with it, man!), they were basically lengthening the standard frames to emulate their drag racing counterparts for the street. Now this worked to a degree, although handling was, shall we say…. interesting, with something like 18 inches more of thin wall tubing trying to be twisted off the engine cradle every time the front wheel changed direction, but as with all things custom, it was tolerated and deemed the price to pay for looking cool.
As is our way on bikerMetric and everywhere in the custom motorcycle industry, we are constantly looking for a new angle on this and a new angle on that in the name of individuality, and as the frames seemed to have been pushed to the limit, next area of attention was the engine and drivetrain, and before we knew it there were seriously tuned diggers; turbo charged, super charged, and even multi-engined versions appeared.
In fairness many of the bigger builders only built these things as show boats and they were trailered to shows. A lot of them didn’t even have internals in the engines but a lot of average Joes looked at these creations and copied them. Sadly they were deathtraps and a lot of nastiness on the roads ensued! Thankfully things calmed down and the digger style died with disco. In that time lessons had been learned and the builders figured that using thin wall, skinny tube for any great length wasn’t the way to go. None of us had multi-million dollar Research & Development plants that we could try our our ideas on and perfect a tube size for a given frame application, so we played it safe and upped the diameter and wall thickness. After all, it seems most engineers will tell you that the fastest way of fixing most problems is to throw more steel at it (take a closer look at any Mercedes or Porsches)!
So what are we gonna do? I figure that we’ll take the middle road and use 1″ 12 gauge CFS 3 or DOM seamless and go through the steps of building a Triumph/XS style chopper frame. 10 gauge equates to more or less 3.2mm or 1/8″ , and 12 gauge is slightly less than that. You can ballpark these thicknesses as pretty much 1/8″ or 3mm.
Where to start then? The first thing you should do is actually be aware of what you want. Seriously! You’d be amazed at the percentage of people who say they want to build a bike and then actually have no idea what they actually want to build. The easy way around this is to do a sketch of what you have in mind. We’ve all seen “Biker Build Off” and the cocktail napkin sketches.
Don’t knock it because some of the tastiest builds on the planet started as the drunken scrawling of someone on a cocktail napkin. It doesn’t matter if you go online and find detailed blueprints of what you want to build, have the drawing/draftsman skills yourself to draw up plans for what you want to build or do a sketch with one of your kids crayons. The point is that you need a visual representation before you start, not only to help keep you on track through the building process, but unless you can just reach up to a rack and pull off lengths of available tubing, some sort of sketch/drawing will be necessary to come up with a materials list that’s in the ballpark. So, on that note, and from experience you will need:
1. Two lengths of tube of the appropriate diameter and wall thickness
In our case 1″ 12 gauge CFS 3 or DOM seamless. A length is 4 metres or 13 feet. The average chopper frame takes between 6 and 7 metres of tube. It never pays to ask the supplier to cut some off a length for you. Buy the whole length, it is always the cheapest option. After all, you can use it up on other stuff anyway and it won’t be wasted.
2. A couple of square feet of 1/8″ and 1/4″ flat plate for cutting out brackets and such.
3. A steering neck
This could be a whole article on it’s own. But in an effort to keep it short, I strongly recommend either getting hold of or making a steering neck to Harley specifications: i.e. 7″ long and sized to take 2″ o/d and 1″ i/d Timken Roller Bearings.
NOT NECK CONES (shudders)! Why? Try this; go into any Yamazukonda dealer and ask for some replacement neck bearings for any model that takes your fancy. When you’ve picked yourself up off the floor and retrieved your now empty wallet and the re-mortgage contract on your house, pop round to your local bearing supply house and ask for a set of 2″ o/d and 1″ i/d Timken Roller Bearings. Yeah, I know!That cost less than a pack of cigarettes! How freaky is that? I think I made my point. Life ain’t fair I know, and it sure as **** ain’t when it comes to *** bike replacement parts. Yes, you might have to get one turned up. There are plenty all over the internet and they’re not expensive, or you might have to turn one up yourself, which is not at all difficult for a competent lathe guy. But in the long run it will make life easier and cheaper to run your sickle by taking my advice here.
4. Rear spindle carriers
Again, this is a subject that could take a lot of space that we haven’t really got. The cheapest way out is some of the flat plate that’s on your shopping list above. The easiest way is to order a pair off one of the many parts suppliers online. There are many out there, plate billet, concealed nuts, square ones, oval ones, the world is your oyster. It’s up to you how you play this. In case when we get further down the road I’ll explain how to make some flat plate types with the only the tools that we’ve equipped our shops with. You’ll like that one.
So to quickly re-cap: We have our attitude set to hardcore and ready to kick some steel ***! We have our tools sitting there waiting for us to get all medieval on the steel. We have the steel tube and various other parts and pieces quivering over in the corner knowing that they are going to get seriously slapped about and mutilated very shortly.
Stay tuned for the next installment, where we get into reshaping the steel into the image on our cocktail napkins!
We’ve spent the last few months getting our shop ready and acquiring tools and bits and pieces. Now it’s time to get busy and put all this stuff to use. Let’s build a frame.
To briefly re-cap from “You’ve Been Framed Part 1,” we decided on a rigid chopper frame to take a XS/Triumph/CB type of motor using 1″ diameter 1/8″ wall CFS 3 or DM tubing. Also recall there are two disciplines that we need to be good at and note the word NEED. They are:
1. Welding! Yeah, I know I go on about it and I make no apologies, but you have to be a good welder. Scan back thru previous articles for my reasoning. PEOPLE DIE WHEN MOTORCYCLE FRAMES ARE NOT WELDED PROPERLY. So nail it down.
2. Tube Notching. This is one of the areas that drives most people nuts when they first get into building frames. Sadly, like welding, the only real way to learn how to do it is to actually do it. After you have the feel for it, you’ll wonder why it was ever so **** difficult, just like welding. I don’t believe in coincidence and I firmly believe that these two relatively easy disciplines are important for a purpose. Knowing them sorts the men from the boys (and the posers). In other words, if you can’t persevere with learning them and getting them right, you shouldn’t be building frames to begin with. Go away and view some ***********. In the last article I suggested you get some cheapo tube and practice, practice, practice your tube/metalwork skills. Hopefully you all took note and can now weld and notch tube good enough to be a member for the next Olympic Welding and Tube Notching team.
We will also need a tool that I forgot in the last techTip, and for this I apologize; it’s an angle meter (pic below). It’s not an expensive tool and they are all over the internet. A great tool, it has a magnetic base so you can just stick it on the tube and read the angle. A MUST HAVE.
Now, where to start? Well, as most of this activity is going to be on or around our frame jig, let’s start there.
First thing to do is to put the neck in the jig at the required rake angle and at the required height. There are a few ways of working this out and it all depends on how precise to you want to be. If you have a state-of-the-art technical drawing nailed up on the wall, then the dimensions are already on there and you just read ’em off and fit the neck in place on the jig. If not, and I suspect this is most of you, then we have to do a bit of calculating. To start with, we aren’t modding a standard frame so we can’t go for a wander around the the next bike meet and find something suitable to measure. We have to think of something else. Well, we did actually start with a sketch on a bar napkin as I recall. Ask yourself these questions:
1. Am I happy with this overall look?
2. Is there ANYTHING about this I would change NOW, before I take the saw to it? If you’re happy with what you have as a design, pin it on the wall.
Okay, now that’s in place and we have a starting point. It might be worth getting a few photocopies and keeping them in a clean place for the duration of the build.
Using your sketch as a reference, you’ve decided you’re happy with how it looks; it’s rake, neck height, seat height, and all that. Now you have to make some metal look like it. Easy!
The first thing is to find a protractor and measure the rake angle on your sketch. This angle is inclined forwards and upwards from an imaginary straight line perpendicular to the ground drawn through the center of the neck starting at the top, and intersects at zero degrees with another imaginary line drawn straight down from your front wheel’s axle.
It’s unlikely unless you have the eyesight of a bird of prey that you will see anything plus or minus half a degree with a protractor. I’d recommend sticking to whole degrees at this stage. For example, if you think you’ve measured 39.5 deg, round it up to 40 or down to 39, it’s your call. It’s not as if we are fine tuning Rossi’s Duke for the next Moto GP. We can get into handling and rake and trail later. Suffice to say at this stage we need to get into the ballpark and see what we have. Therefore, for the sake of our exercise, let’s settle on a rake of 38 degrees – not Trent’s crazy 51 degree rake pictured in his helpful diagram – which is not too outrageous and should in theory give us a workable trail when we come to figure that out.
Now how about height. How the **** do we work that out from a cocktail napkin sketch?
Well, it might be a rough sketch on a beer stained bar napkin to everyone else, but to us it’s a detailed blueprint and has a wealth of information all over it.
Believe it or not, the first measurements we can nail down are the axle heights. In our case we are going for a 21″ front wheel and an 18″ rear. A 21″ front has a rolling radius of 26″, depending on the tire. It can vary by maybe .25 to .5 of an inch but you’re safe saying 26 inches in this case. An 18″ rear has a rolling radius of 24″, and the same rules apply there as to the front. Now, what does this tell us apart from what sizes the wheel/tire combos are? To start with, if we divide these sizes in half we get our front and rear axle heights. If we decide on a ride height, let’s say five inches at the lower rails, we now know that the rear axle carrier in the jig can be set to seven inches from the top of the jig bottom rails. Remember that the top of the frame jig rails equates to the bottom of the lower frame rails.
Important dimension #01 sorted out, so let’s move on. If we know where our bottom rail is going to be (five inches off the floor), and we know that our front wheel is 21″, then we can calculate from our sketch the height we want to try our neck at. I say “try” because until we have completely mocked this up in steel and are happy with it, it’s all hypothetical, but this is how we get there. If we measure the front wheel on my sketch, it comes out at two inches, there’s my scale, 2″= 21″. From this I can pretty much determine almost everything else. From my sketch I can measure the top of the neck and it’s at 2.5″ from the bottom of the frame rails, which scaled up gives me a distance of 31.5″. I’m gonna round that up to 32″ just because of pencil line thickness, but it also takes out an unnecessary fractional measurement that we don’t really need.
We can now put the neck in place at the right angle and at the right height. 38 degrees of rake and 32″ from the bottom of the bottom rails to the top of the neck. So far so good…. What’s next? We have our two ends – the neck at the front and axle at the rear – almost in place, but we don’t actually have the distance between them yet. We do have the neck nailed into place though and my logic tells me to work front to rear, so let’s pull the engine out from under the bench and roughly site it the jig. Again, using our sketch as our reference we need to chock it into place using bits of old timber/brick/whatever, but the important position is 1″ up off the frame jig rails to account for frame tube thickness.
Now if you remember back to previous tips, I suggested in every one of them that you acquire a half dozen or so three foot long pieces of 1″ dowel. I distinctly remember going on and on about it. Yes, I did! Okay, so I didn’t, and it’s too late now, but we need at least one at this juncture, so run out and get some at the hardware store or cut off the handle of your broom.
(waits…. gets a beer…)
Okay. Now lay the broomstick/dowel against the lower half of the steering neck and the front of the engine. Step away and see what that looks like. Yep, you guessed it, we are now nailing down the angle of our downtubes. Position it in such a way that it simulates your sketch and look where the front engine mounts are going to end up. While not particularly critical, the smaller any plates can be in the engine mount world the more solidly mounted your engine is going to be. When you’re happy that it looks good, measure the angle, keeping it relative to the neck for simplicity, and you’ll find you end up with a measurement somewhere between 67 and 72 degrees. Write it down because it’s the first bend we’ll be doing later.
Having nailed down our neck and engine position, we now need to sort the rear engine mount and seat post position. Again with our broomstick/dowel, position it behind the engine close enough to imagine your engine mount plates/slugs/whatever the system is for your particular engine, but not so close that lifting the engine in and out would be hampered. This is a good time to break out the duct tape. Take your first broomstick/dowel and cut it to fit more or less where the front downtubes are going to be. Cut the second one that you’re using to mock up the seat post with a tad longer, about two inches, and tape that in position. You may want it straight up, leaning forward slightly, or leaning back. It’s your choice, however you fancy it. Now tape it into place. Take another broomstick and tape it into place as your backbone from the neck straight back through the seat post position and tape that in place when you’re happy with the angle. Stand back and take a good hard critical look at what you have done. It should more or less look like the front half of the frame you dreamed of and sketched on your beer stained napkin.
The next step is to mock up your battery box, decide where to place your oil tank (for ease of explanation we’ll stick with the conventional under-the-seat-slot), electricity box, handgun and knife storage, etc. Mocking the battery box up in the jig also gives us the position that the lower rails will kick up and meet the rear axle carrier. Again, break out the duct tape and the broomstick/dowels and mock that tube up into position.
Now we are ready for the top tubes. The top tube (AKA: backbone) now needs to be mocked into place. Again with the duct tape and dowels, mindful that this needs to come down to just past the top of the seat post. Play with this angle to get your desired look. You now have a position where the frame top rear rails are going to start from and head down to the top of the rear axle carrier. It’s difficult one to mock up with a broomstick because it has a bend in it, and really hardly worth the bother. The only real reason for doing this is to be sure the angle of the rear rails isn’t the same as the backbone angle from the neck. Now sit back with a cold one and see if what you have mocked up in front of you is what you’ve been dreaming of.
Now put the kettle on just in case I pop ’round to see how you’re doing! Next time we turn the broomsticks into bedknobs…
Picking up where we left off with two concepts to start; confidence and common sense. “What’s he babbling about confidence for,” I hear everyone ask. It’s simple, as in most things, if you feel apprehensive about doing this then practice, practice, and practice with cheap steel tubing like water/plumbing pipe or whatever until you feel happy to get to work properly. That’s common sense. Remember that you will be riding this creation and you don’t want it failing on you. Also, which is arguably worse, you will probably at some time in the future sell it, thereby putting the results of your skills into someone else’s hands. If your confidence is lacking and you’re feeling apprehensive, build your first frame following this series of articles out of some cheapo water pipe. It won’t be wasted. At worst you can flat black paint it with a rattle can and ask your local bar to hang it off the ceiling. As with our power tools tip, build up your confidence with this stuff and feel happy you can tackle the job before you start.
You should now be looking at a pretty accurate mock up of the frame design you dreamed up on your napkin/CAD package/drawing board. My suggestion at this stage is this: You played with your sketches and drawings for a long time to get your ideal look and style, so don’t rush it now. Take some time outs to look long and hard at your mock-up and don’t even glance across at your steel and parts collection until you’re 100% happy with what you’re looking at in your jig.
Your first bends should be the downtube bends that send the lower rails up to the steering neck. Measure the angle on your mock-up carefully and double check it with the one you wrote down earlier. If they’re different, no worries, we’ll tweak it soon. We are making two of these, so measure carefully the length of tube required. We have to go from the neck curve down past the engine and back to the rear spindle carrier. Measure this length and chop off two lengths about six inches longer than the measurement. With this type of frame that we are building, we can make the distance between the rails (from the forward bends backwards) the same all the way back because we are using no bigger than a 130mm tire. Things can get complicated when the lower frame rails have to be bent in two directions (up and out) at the point where they kick up to meet the rear spindle carrier if we are using wide (generally wider than 150mm) rear tires. Many builders end the lower rails just past the seat post and use two hoops as the upper and lower rear rails. Thankfully, as this is a somewhat debatable practice, we needn’t be getting into it with this article, although we may in the future.
Having completed the mock-up and before we put a piece of tube into our bender, we need to make a little tool as a guide. Chop off about 18 inches of the tube you are using and create a line around it’s circumference with a permanent marker, being sure you can see it clearly. Place this piece in your bender with the line at the bender’s start point and bend it through the number of degrees you need those bottom bends to be. Now, look carefully at the other end and make a line around where the bend ends. This is not the easiest thing to judge, and the best way to do so is subjective. One must simply be able to tell. Look at it and get the feel for it, and make your mark. This is now our homemade gauge to judge where to start our bends. Bare with me all and will become clear as we progress.
You can take the engine out of the jig now and being careful not to disturb any of your mocked-up pieces of tube, take the bend mock-up you just created and lay it carefully against the downtube where the bend should start and tape it in position so it follows the downtube and the lower rail perfectly. Now measure the distance from the top line on the bend template to the neck, add two inches, and that’s the position of the first bends on the downtubes. Mark these tubes in the same way as our template with a permanent marker and bend them identically. You can now take the broomstick out of the jig and replace it with both of these tubes. Just for the moment lean the tops of the downtubes against each side of the neck, as we are going to wander off on a slight tangent for a minute or two.
Depending on how detailed you’re drawing or sketch was, you may or may not have gone into great detail on how the downtubes and backbone meet up with the neck although it is very important. There are various ways of doing this. Some are good some are not so good and some are downright scary. What we need to achieve is to have as much weld area as possible. Look how Harley achieves this in this pic:
The down tubes meet the backbone and only the backbone tube is directly attached to the neck. Below the backbone is a plate structure that boxes it all in and makes for a very solid and secure joining of all the components. It’s a very efficient way of putting it all together, although the downside is if the neck area is in plain view and not hidden below a tank, it can make the frame look very bulky at the front end. It’s good with a lot of weld area on the neck, but we won’t be doing that on this frame.
Another popular method is to make all the tubes meet the neck. This is okay but it can be a bit risky as the amount of weld area achieved this way isn’t very much and we have a few hundred pounds of bike and rider hanging off it.
Let’s not do that. We can do a lot better with very little effort.
A third way is to join all the tubes at the neck as above, but with some gusseting. As you can see from the images below, this not only is a very neat and tidy join and it maximizes the weld area that is available. Not only are all the tubes welded to the neck all the way around their circumferences, but the gussets on each side of the tubes are 1/8″ plate which is pretty much the same thickness as the tube wall. This is important because the weld will be stronger if the two pieces being joined are the same thickness. It’s a pretty safe bet this particular neck isn’t going anywhere under any conditions on the road. We’ll be doing something similar.
Now we have our downtubes sitting on the jig, leaning against the neck. Make sure they are touching the neck towards the bottom, ideally about a quarter inch or so above the bottom of the neck at their lowest/most forward point.
The next thing to do is to nail down the distance between the lower frame rails. This is determined by a number of ways. In an attempt to keep it simple, we can distance our frame rails at 8.5″ between the rails, or 9.5″ on centers. This distance is needed to clear a 530 chain on a 130 wheel tire. The sketch below paints a thousand words. The most critical measurement is where the centerline of the sprocket lies. In this instance we are leaving ¼” ish for the chain-to-tire clearance.
Looking at that sketch it’s easy to see how to get to the dimensions we need to get our lower frame rails right. I’ve put a 200mm tire example in it to illustrate the procedure a little better. The trick is to accurately measure the width of the tire you’re actually going to be using (my Metzler 200 is actually closer to 190). This is crucial to getting the wheels in line with each other in the frame. As far as the front is concerned, as long as the neck is firmly in the jig and the forks aren’t bent, it looks after itself centreline wise.
The rear is a different ball game and it’s very easy to get it wrong. We need to know what size our chain is and how far away from the outside edge of the tire the sprocket is. Remember this procedure when you’re using a donor wheel and the sprocket is already fitted to it. Give yourself a quarter of an inch clearance between the edge of the tire and the and certainly not less that 1/8″. Space the sprocket out with washers if need be. A “standard” flat washer is generally 1/16″ thick and don’t forget how worn chains move sideways as well. In the example above, the sprocket center is 3 and ⅜” off center and a 530 chain is one inch across, give or take a thousandth of an inch or two. To be honest, if you work with that chain measurement for everything, as a rule when using a smaller sized chain you will know you have enough clearance.
As we can see from the sketch with a 130 tire, the center of the sprocket is 3 and ⅜” from the center line, given that the chain is 1″ wide and the outside of the chain is 3 and ⅞” from the center line. This makes the inside of the chain 2 and ⅞”, double this distance and we end up with a usable width of 5 and ¾” and if our 130 tire is 5 and ¼” across, we have the necessary ¼” of clearance between the chain and tire. If we clamp our rails in the jig at 9.5″ on center (8.5″ between them), we have ¼” clearance between the tire and the chain and ⅜” clearance between the frame and the chain. It’s always better to start as close to the tire as you can get with the option of coming out ⅛” or so if needed to help with the engine sprocket line up.
Lean the frame rails on the steering neck and mark up the front/top of the front rails for coping onto the neck. We have to do this before we bend the lower rails up to meet the rear spindle carrier. Until the front downtubes are coped and tacked in place on the neck, we are unable to determine the top of the lower rails, which we need before we can bend them up to the rear spindle. Having clamped the rails into place, cut two lengths of tube with each end notched to fit between the lower frame rails. Again, it’s very important they’re cut the same length but don’t tack them on yet, as we will be using them later. For the moment they will act as distance pieces to keep the lower rails straight and parallel to each other. This is best done with a 1″ hole saw in the pillar drill and is easy enough to work out. We need them to be 8.5″ between the inside of the cope. See the sketch below:
The center marks on the sketch are where you “center pop” and drill through with your 1″ hole saw. Mark a line along the length of tube at the center to ensure that both your cuts at each end will be on the same plain. Clamp each in your drill press and drill ’em through. Voila! Now place these in between the lower rails to keep them parallel and straight to each other, and clamp the assembly down.
I can see even the front row falling asleep on me at this point, so we’ll break here and continue in the next installment, should Trent get it up in a timely manner. Get the coffee brewing and I’ll try and pop ’round to mark your efforts…
g’day everybody. bikerMetric has a new contributor and his name is alex chopperbuilder. he’s going to be working in the techTip department and every two weeks he’s going to hit garage builders with information to assist in their builds.
hitler had goebbels, bush had cheney, alex has me.
just like goebbels presented the german masses with messages of how everyday life under bolshevism was miserable, framing a blueprint for cheney to present the american masses with messages of how everyday life under terrorism would be miserable, there must be a few who say **** it, **** you, i wanna build a bike. no matter what.
you can’t ride a bike in a suit. not without deep cosmolopsychologicated ramificatorships.
yeah, i’m looking at you, confederate.
and yes, i just made up some funny hillbilly-sounding words.
here we go:
You’ll need a lot of things to start, so I thought it best to begin with “where” before bravely stepping into the world of “what.” Yes, however you want to play this game, you need somewhere to do it.
This article is aimed at the guy who has a garage or shed next to the house, a buddy who has one, or a small unit somewhere. That’s not to say we aren’t going to look at what the pros do in their places and get some tips, but this isn’t an issue of Motorcycle Dream Garage.
I’ll keep this affordable and filled with necessary essentials. You won’t be taking out second mortgages to get thousands of dollars worth of computers, software and a water jet.
A lot of fine bikes get built by guys under sheets and tarpaulins, in lean-to’s against the side of the house and even in the house itself. A workshop dedicated to your passion isn’t necessarily a necessity to the end result but I have yet to speak with a guy who has built anything out in the yard or under a tarp who would not have preferred to do it in a nice warm workshop.
A dream garage isn’t beyond the realm of possibility. All it takes is a big budget, but I’m prepared to bet that if you could afford to set up a workshop like that to build your pride and joy, you wouldn’t be reading this article.
The first thing we need to ask ourselves is “what do I want to achieve?” The answer isn’t obvious. It’s subjective. Building a bike isn’t the complete answer, either. Building a bike is a step-by-step procedure that encompasses a lot of processes, and to be realistic, if we want to do them all ourselves we need a lot of different spaces dedicated to different disciplines including welding, machining, polishing, painting, and more.
More realistically, we will have to expect our space to a multitasking area, which means some pretty serious organization of both procedures and storage of stuff, and dare I say cleanliness.
Answering “what do I want to achieve,” is quickly followed by, “how much space do I need?” The answer is “how much have I got?”
For the purpose of these articles, we are going to presume you have a space that equates to a normal single car garage. If you have more space, great, you’ll find information here on appeasing your girlfriend by buying her a puppy.
EDITOR’S NOTE: do not Google “naked babe puppy” with moderation turned off.
If you have less than a single-space garage, stay tuned!
You need a space at least as long as the finished bike that must include a couple of feet on every side for a bench. That means a space more or less 12 feet long by about 8 feet wide. Keep in mind this would really be the minimum and this amount of space really doesn’t have much room for storage of parts and tools.
Now that you have the space, all you need is to prepare that really old set of springers that you found two months ago after scouring the planet since before dinosaurs walked. They’ve been sitting outside going rusty, which they will do no matter how much grease or WD-40 you spray on them, until you’re ready to actually bolt them on to the bike in your first of many trial build ups.
If you only have a shed to trick out, look into the possibilities of putting a covered deck on it. This will give shelter for the times when you must scoot the rolling chassis out for one of the many occasions that entails scooting the rolling chassis, such as to place large parts like the engine, tanks, handlebars, and wheels upon it, and to stare at it at a distance while drinking beer.
Also, look for alternative spaces nearby that would permit storage such as garage cabinets, attics, basements, and living room corners where your Rock Band 2 drum kit collects dust. I’m loathe to suggest anywhere in the house, unless you live alone, or soon want to!
These are the “build up/try out” stages which will eventually become the final assembly of all the shiny and painted and polished stuff that you really don’t want lying all over the place.
In our next episode we’ll look into equipping your space. I’ll show you what tools you really need and how to make it a space that you not only want to spend time in, but that will allow you to maximize your own skills and enjoy what you’re doing. That’s a pretty important aspect to the whole thing…
.
2. Frame and tube work
3. Sheet metal and tins
4. Machining
5. Sub-assemblies: motor rebuild/repair, electrical, carburetors, front ends, brakes, etc.
6. Paint, polishing and plating
7. Final assembly
The first thing to jump out at us is that we are going to need “clean” and “dirty” areas. Lets go back to our available space. Remember we drew a line in the sand and decided that for the purpose of these articles we had a single bay garage space available. My apologies if you have less, I’ll leave the creativity of your workspace to you but will remind you that less space means the same things are going to apply but you will need to scale some of it down and become very adept at organizing.
The first thing to consider is not tools but benches. However much of the work you are going to do yourself, you will really need to have two benches or “bench areas” This isn’t a luxury, it really is a necessity. Pretty much all fabrication is classed as dirty work. From bending tube for your frame to cleaning, repairing and assembling mechanical parts. We’ll use saws, files, drills, sandpaper, and much more. All of these tasks produce undesirable by-products to our “clean” assembly side of the garage. Get the picture? Ok, so laying out our benches and therefore our “clean” and “dirty” areas suddenly becomes very important.
Check out the image above. We’ve taken a pretty standard garage space with a normal roll up garage door at the front and an entry at a rear corner. There are benches all around. You’re all clever folk and I don’t want to get into exact instructions here, but by looking at the picture you should get a good idea as to what I find to be the ideal bench set up for bike building. Now you can see where the ideal minimum workspace comes from. The floor will inevitably be concrete. If not then it might be timber, or if you’re lucky like me it may simply be good old flattened earth. None of these options are acceptable.
A concrete floor constantly creates dust and when cleaning and sweeping the dust will invariably impregnate your more delicate parts, doing them no favors whatsoever. DUST IS YOUR ENEMY!
If the floor is concrete, the minimum you must do is paint it. There are plenty of floor paints out there, but remember if you paint it with cheap paint, you’ll paint it often! If the floor is timber, again the minimum you need to do is paint it. A good and inexpensive fix on a timber floor is to get sturdy plywood nailed down to get a decent and relatively smooth surface and then paint. If, like me, you have a pounded earth floor, you must pave it with concrete and of course, paint it.
What you must remember is that the floor really needs to be flat for safety and easy to clean. a flat and clean floor is easier to find those mixture screws that just rolled off the bench. A good and easily maintainable surface is tile. The adhesive PVC/Lino types are nice or ceramic tiles if you’re feeling ritzy and confident that you won’t be dropping anything heavy on them! The tiling option is in lieu of paint. Remember that when we are in our assembly phases, major final assembly or sub-assemblies, we are going to be scooting back and forth on our old office chairs and it’s ****** annoying when you can’t scoot straight due to a lumpy floor. Whatever you decide, make your floor flat and easy to mop, which basically means waterproof. The methods I have suggested are the best ones I know of, but by all means feel free to comment below and expand my knowledge with further ones.
Onwards and upwards to benches. We need two narrow benches, one running down each side of the garage and an open area between the two, which by no coincidence whatsoever is enough for us to walk around our soon to be growing pride and joy. At the risk of sounding a bit patronizing here, I will mention that the benches really need to be solid. This means that unless you have a large budget and can afford to shop with the Formula 1 workshop suppliers, you will be building them yourselves.
Welded steel frameworks with thick plywood tops are fantastic and sturdy, and 3″ by 3″ (or 4×4) legs and frames solidly screwed together, work perfectly. Solid wood benches will do the trick as well. I have to leave that to you. Personally I favor solid timber legs and frames and cheapo kitchen worktops because they are easy to keep clean and tidy, which makes losing things like your idle jets a lot harder to do!
Did I mention they should not be too deep? I’ll come to that in a minute….
One side will be your “clean” side and the other will be “dirty.” For the clean side, I strongly suggest that you make the bench approximately the height of your dining table. bout 30 inches high is good. A very large part of your clean work is actually assembling sub-assemblies such as the engine, gearbox, carbs, electrical stuff and more. You’ll be more attentive, more comfortable and be able to do it for longer if you’re sitting comfortably for a **** of a lot of this stuff.
Take a minute and try this experiment. Sit at your dining table, upright, back straight and see how far you can reach across without straining. Bet it’s about 24 inches before you really have to stretch. With that new found knowledge under your belt think about why you would want to make your bench any wider. Can’t find a good reason? The thing is that the larger the bench area the more **** you are able to accumulate on it.” Remember that we are trying to achieve an enjoyable workspace that is a pleasure to be in and work in. On this side try to keep the bench completely clear underneath.
Look at the image above. The ideal is to be able to scoot back and forth along the length of the workshop without smacking your knees and ankles on stuff piled under the bench.
For seating, make a couple of them. Old office chairs will do, but take the backs off as scooting back and forth around your bike as it comes together gets a bit trickier as it gets larger and you don’t want to be dragging anything around behind your back that you shouldn’t. I tend to think of the clean bench as more of a desk than a bench. I like it well lit, completely uncluttered and with hand tools within easy reach.
The left hand bench is at a relatively standard height, kitchen counter top high, which is more or less about three feet tall. This is a good height for work done while standing and is pretty much everything you’ll do on the “dirty” side of the garage.
Hammering, prying, filing, and more are all done best when we are standing up. On this side somewhere we will need a good solid vise. Think about the mounting and support of it, as you will tend to use the vise as a grip to hold stuff whilst you hammer things apart/together. Mount it sturdily. Also think about its position. I suggest in a set up like we have in in our one-bay garage that you mount your vise about two thirds of the way down the “dirty” bench towards the front door.
This side is where you want to organize all your storage. Under this bench is dead space and space is something we don’t have an abundance off. Parts bins and large stuff like a compressor, or welding machine should be under this bench. If at all possible attach some sort of doors here. Even if it’s only curtains, remember don’t use material that bursts into flame if you walk past it with a cigarette!
Other work we will be doing on this bench will include welding, so it’s good to cover a section of the bench, just a couple of feet, in metal. Steel is good, a piece of 14 or 12 gauge screwed down to the surface will be a great help when you weld anything. Tack a small piece of angle iron to the back of it as an “earth post” as well. That way if you weld something small the bench can act as the earth and you have one less clamp/cable to think about when you’re welding. Screw a length of angle iron to the wall as well. Do this above your head, over six feet high. This is to place all your clamps and mole grips to so they are within easy reach while you’re working. If you suddenly find you need another clamp in a hurry they are there right in front of your face.
A bench grinder, actually if possible have three of them! I’ll explain…. They are pretty cheap so there’s no need to go to the big expensive suppliers for these things. A good bench grinder is a savior and they can be a bit of a multi tool.
Another important piece is a wire brush and a polisher. I suggest that you fab up three free-standing platforms about four feet high if you are able. This way you are not constantly changing stones and mops. On one have a course and a fine grindstone. Use the second platform for a steel and brass wire brush and the third for the polishing mops. There isn’t anything at all that we do on one of these three tools that can be remotely thought of as clean work. Having them on their own stands facilitates moving them outside whenever possible to do the dirty work out there.
Remember to keep it narrow. We are working on and/or building motorcycles. The parts and assemblies are not the size of car stuff and we don’t need massive benches to work on. You’ll need the space in the middle of the workshop where the bike will actually be assembled, and narrow benches help out in this regard. I’m trying to keep you from having to get on with a particular task you’ve set your mind to achieving one day without having to clear a space through mountains of **** to do it.
I think that’s about as far as I need to go regarding benches. Just remember two basic rules:
Rule #1: Keep it clean and tidy by putting things away.
Rule #2: Keep it clean and tidy by putting things away.
Seriously though, I can’t say this often enough. These rules need to be applied constantly. You might feel that you’re spending more time cleaning up than building and sometimes you will be, but trust me that in the long run it will be quicker and you will save a shitload of time, not to mention a shitload of money on parts you won’t have to replace because you haven’t lost them.
So what else do we need in this shop?
Lighting! Yeah, I know…. No ****, Sherlock. It seems obvious but put your Hands up now and be honest….. How many of you out there were going to go down to the nearest Kwik-E-Mart and buy a long fluorescent light from Apu? Don’t let me stop you, but before you do please keep these facts in mind. I won’t go into great detail, by all means research what I’m about to tell you yourselves.
Fluorescent light is very bad for you.
It’s bad for your eyes and it’s bad for your skin. The humming is maddening if you’re quietly working. Last but not least, it’s really bad for morale! Really. It is and that’s a big deal! Now I know we’re rough & tough bikers that laugh at danger and smile at the tattooist needle. You can check it out yourselves but fluorescent light really is a depressing light and countless studies have proven this to be so. Even Navy submarines have completely removed fluorescent lights because they were proven to be a contributing factor to submariners suicides! Air Traffic Controllers have the highest suicide rate by profession in the world. Air Traffic Control Towers no longer have fluorescent lights and it has apparently helped.
Carefully bear your lighting in mind and plan it out when you run your power circuits for the sockets around your garage. I favor halogen spotlights. They are as reasonably priced as fluo stuff and can be placed to suit different work spaces. You can have a lot or as little light as you like. Have a couple of office-type anglepoise lamps handy as well. These guys are really useful for that close up work like cleaning cylinder heads and carbs.
Now let’s look at storage and think about it carefully. You will know by now which tasks in your build you’re farming out (if any) and therefore what you need in your shop to do the stuff on your list. For example, if you plan on painting the bike yourself you know you need a compressor and that will need housing somewhere. I’ve already hinted that it would need to go under the left hand bench somewhere, but space and neighbors/family permitting it could actually go in its own little lean-to building on the side of the garage outside. Bear in mind they can be noisy. If you’re planning on doing all the welding, then a place needs to be found for the welder. Again under the bench has been suggested and that’s probably the best place. It does need to be kept dry and as clean as possible.
The point I’m getting at is that all these different disciplines carry their own levels of baggage in the way of consumables and accessories. We will also accumulate parts along the way to the finished build. Space, especially storage space, often becomes harder and harder to come by. Shelves are good but kitchen-type cupboards on the wall at eyeball height are better. Especially for keeping things separated and clean. Don’t store anything heavy up there as there’s not much that will lower your spirits to the height of a wiener dog’s ******** faster than something heavy falling out of a cupboard and bashing you in the noggin when you’re concentrating on grinding valves. Store the heavy stuff and parts below the bench. I find it extremely useful to store bagged and labeled small parts in cupboards.
The cheapest way of building a low-cost custom bike is to be really **** about your parts storage. An example is the rear fender on my current build. It’s going to require four 10mm Allen Bolts, eight nylon washers, four Belleville washers, and four Nylock nuts. These are sitting in a zip-locked bag ready for use. I do this for every assembly and sub-assembly. The amount of time and hassle it saves is incredible, not to mention the monetary savings because I only acquire these things once.
This is as far as we’ll go on about laying out your basic workshop. We’ll do one more part on setting up your home garage that will focus more on the tools needed for various disciplines.
Stay tuned mofos (as Trent would say) because believe it or not, the tool universe does not revolve around a certain very good factory in Milwaukee…
.
[EDITOR’S NOTE: Yes, this was to be a three-part series, but Alex decided to divide tools into hand tools and power tools. Part 4: power tools coming soon…]
What we need now is to cut down on the echo and reverberation in your new garage caused by the use of tools. Before you all go running off for Google to find the nearest Snap-on van, like I know you were all about to, let’s have a brewski and sit down on one of our old office chairs at our new and immaculate bench with a pad and paper and start makin’ some notes. Have a nice pause…. How good does that feel? I’m not the sort to say I told you so, but hey, I told you so!
At this stage it’s very easy to throw caution to the wind and make great long lists of all the shiny spanners and pullers and tools you remember seeing in Billy Lane’s workshop on Discovery. Slow down now and take a sip of that brew….. Tools are expensive, and good tools are more so. The first thing to do is to list the basics that everybody needs in their toolbox, no matter what skills you possess.
For the purpose of this article I’m going to suppose that you all have empty toolboxes. So what’s obvious? I’ll list them:
1. Spanners and Wrenches
2. Screwdrivers
3. Pliers
4. Hammers
5. Grips
6. Socket Set
7. Torque Wrench
Obvious? To some they are, but let’s put things into perspective item by item:
1. Spanners and wrenches: As cheap-assed bikerMetric readers I’ll assume you’re on a tight budget and can’t really stretch to combination spanners. You’ll have to buy two sets of open-ended wrenches to start.
“Two sets!?” I hear you cry. Yes, two. It’s hard to tighten or loosen a nut and bolt with only one.
You will need more, but to start get two sets of either Metric (6mm through 32mm), or Imperial/Standard (3/16″ thru to 1¼”), depending on whether your project is old Brit iron, American (Standard) or anything else (Metric). You will need a few that are bigger than as the project progresses, but it’s better to deal with those when they are required.
I’m afraid you will also need to buy a set of ring wrenches as well. Here’s why; you will severely damage a nut or bolt head of a really tightened-up and stubborn nut and bolt trying to release it with an open-ended wrench. This is why the ring wrench exists. People loosen with open ended wrenches because they are generally faster and you aren’t really subjecting them to massive amounts of torque. Likewise when tightening.
Now you have a dilemma. At the top I said if you were on a tight budget to buy open-ended and not combination wrenches. This is where you’ve got to decide on whether to buy three sets of spanners/wrenches or just two sets of combination wrenches.
[EDITOR’S NOTE: SEND $9.99 TO FIND OUT HOW! DON’T DELAY!]
Yeah, you got it, this is why combinations are more expensive. My recommendation is to buy the combination sets. Buy good ones if you can stretch your budget to it. The reasons being that you will have these things forever hopefully and that good spanners not only feel nicer to use (it’s true) but they are actually easier to use because they actually fit the fasteners properly.
From experience over the years I have come into possession of many spanners. I have Snap-on, Britool, Craftsman, Facom… You name the brand, I’m pretty sure I can find it in my box. As well as thousands of others that have been picked up off the supermarket shelf/got free with a roll cab/been given to me, et cetera. The point is this, I only go for the good stuff out of my box when I’m working without thinking. The good spanners, and I include all the above makes in that statement – yes I know there are others – just feel so much better when you’re using them. There are two tools that I will always blow a budget with and high-quality wrenches is one of the two. Trust me, buy good stuff with these. You can save money on other stuff.
2. Screwdrivers: It’s really cool to have a nice set of Snap-on screwdrivers in the box because they really are a pleasure to use. But if your budget won’t stretch to them, don’t bother. Save a few bucks and get a couple sets from your local tool supply or auto parts shop. Be comprehensive and get a good assortment of flat blades and Phillips heads. Also get “stubbies,” both flat and Phillips heads. A good multi-head ratcheting screwdriver with all the bits in a case can be a godsend, but don’t fret about screwdrivers, we don’t really use them that much.
3. Pliers: Again, I wouldn’t get too carried away with makes of pliers. Having a top notch set of side cutters is worth it and a pair of long nose and needle nose pliers as well but as for all the others, fill up with the bargain gear and save some money. They are tools that don’t get masses of use. The tools that matter are the wrenches mentioned above and if you have the good ones I mentioned you’re laughing because you know.
4. Hammers: Today it seems there are two makes of hammer; Good and ****! You can tell by the price. A good hammer isn’t actually expensive today but a **** one is cheaper than a crack whore with no teeth. The lesson is don’t buy cheap! I hear this said a lot about tools in general, and it is a good policy if you can afford it, but it really does apply to hammers.
We need to start with a good weight lump hammer and a good ball-peen.
I like Stanley hammers, but to be honest if you’ve heard of the make you should be safe. Do not buy a hammer that either has no make marked on it or a make that you’ve never heard of. I have seen large pieces of hammer head do serious damage to someone other than the person using it. Cheap hammers break and they break into dangerous sized pieces. Like wrenches, you can tell much about a hammer simply by picking it up and swinging it around a bit. The weight will feel well-proportioned and it will feel relatively balanced in a way that makes you want to hit stuff. Other types of specialty hammers we will deal with later.
5. Grips: Molegrips, or vice grips as I’ve heard them called, are a must, especially if we are going to be doing any welding (and we will in later articles). There really isn’t any substitute. As with hammers and wrenches, buy a brand that you’re familiar with, not an inexpensive nor nameless variety. I include G-clamps in the grip category. With these get half a dozen or so in various sizes and you’ll be set.
6. Socket Sets: This is tool #2 that I can blow a budget with big time. The cheapest way to buy socket sets, is, funny enough, to buy complete socket sets. Taking this route means you end up with a very comprehensive set of sockets that look really cool in the top of your box, but contain a lot of socket sizes you will never actually use. If money is tight, then go for a socket set from your local tool/auto supply store to start with, but I would recommend putting your socket set together piecemeal, and buying what you need individually.
Another other point to note is that the main article you’re buying with any socket set is the ratchet itself, and believe me, using a nice ratchet makes the job so much more pleasurable over using a cheap one that the difference is hardly believable. Like man folks who started their mechanical lives in the garage industry, I had an account with the Snap-on man, and like everyone else I over-spent massively and mostly on spanners and ratchets.
I have to say, and I must emphasize that this is a personal opinion but is based on many years of experience with other top makes, that the boys from Kenosha, Wisconsin make the best ratchets out there. It’s not really surprising as they did start the ball rolling when the fledgling company manufactured and marketed ten sockets that would “snap on” to five interchangeable handles. Hence the name, Snap-on. That was in the 1920’s. These boys have been at it for a long time and it shows. If you can stretch your budget to buy their 1/4″ and 3/8″ drive ratchets (or 6 and 12mm), you won’t be sorry and you’ll have them forever.
Likwise with extensions. Get good ones and have a few different lengths, from very short, like 2″ to 12″ long. You’ll be amazed how much they get used.
The only other items not to buy cheap in your socket set are the Impact Sockets. DO NOT EVER BUY CHEAP IMPACT SOCKETS. I’m not even going to go into why. Really. I’m not!
As for the sockets themselves, quite frankly, over the years (and I shake myself for writing this but it’s true) I have found that if I abuse a socket enough, it will rip itself apart, whatever the make. I primarily refer to 12 pointers. six pointers can of course take a phenomenal amount of abuse, but are not so versatile in hard-to-get-at places. The last few years I’ve been using any old socket that I can get my hands on and they work as well as the really expensive ones if I treat them with respect.
I know that all tools should be treated with respect but we don’t live in an ideal world and let’s be honest, we all have our off days. There are mainly three types of sockets to consider; A) normal everyday sockets we see in everyone’s toolbox, B) long reach sockets and C) heavy duty (black) sockets that come in normal and long reach.
Personally I wouldn’t go rushing out spending on these wily-nilly and buying entire sets. Buy them individually as you need them and you’ll be amazed how quick you’ll build up a really comprehensive and useful socket set. As you need them you can expand with Allen Head sockets and Torx bits. If money is an issue and your project doesn’t have any Torx Head bolts then it’s a bit of a waste, really. The last thing to include in your socket set is a good breaker bar. it’s not an essential because there are always pieces of pipe lying around that we can lay our hands on to extend the length of a spanner, but a useful thing to bung on the Christmas or birthday list, and an absolute godsend when the last guy to lock up you rear spindle nuts did it with an air wrench!
Lastly I am going to mention things that are so basic I forgot to list them above. They are:
Allen keys, wire brushes, pry bars, tire levers, a utility knife, a solid and sharp pocket knife, and rags. In fact get yourself two laundry baskets, one under the dirty bench for dirty rags and one next to your clean bench full of clean ones. I **** thee not, YOU CAN NEVER HAVE ENOUGH RAGS IN THE WORKSHOP, and no I’m not sorry for shouting at you. It’s too important for “pretty please.” Buy good ones that are white, and wash them first. If you do this, they last a long time. The red ones are cheap, suck, and stay covered in oil no matter how many times you wash them.
7. Torque Wrench: This is the last most important hand tool you will need. As with hammers and a good socket handle, a solid and well-made torque wrench from a name brand will do you best. These are used to gauge exact tightness for various applications from transmissions to forks, and a piece of **** is going to screw your build up faster than a stalker can boil your puppy. Over-tightening can be a very bad thing and cost a lot to recover, so beware the bargain torque wrenches. I prefer calibrated clutch mechanism torque wrenches, as once the desired torque is met, the clutch slips and you can tighten no more.
I think that about covers the basics. Next time we’ll look at the power tools that come in handy, including welding and compressed air tools. Also, I’ll cover what we’ll be needing if we’re going to venture into that mystical black art that is frame construction. Yep, we’ll have a look see at tube benders and learn now to set up a frame jig. So until next time, Au revoir!
There, that wasn’t hard. See you next week with Part 5, “The Joke’s on You!”
Oh, you want more? All right, I jest. Of course there is more to it so here we go.
Drills come in all shapes and sizes. There are drill press (AKA pillar drills) that come bench mounted and free standing. There are power drills and there are there are cordless drills.
Drills, like spanners and ratchets, are one power tool you really don’t want to buy cheap. When it comes to a drill press, it’s actually hard to buy a crappy one, because the makers don’t cater to the home handyman market so they all tend to be pretty good. If you have the space in your shop, get the biggest one that you can afford. Do this especially if you’re going to build your own frames and want to be notching tubes. Failing that, get a bench-mounted version and again, get the best you can afford. Once you have it set up, you’ll be amazed how much you use it.If you don’t like how it works, swap put the head bearings on your cheapo and be amazed at the difference.
Power drills:
These are the sort you plug in and hold on to. WARNING WILL ROBINSON! There is so much **** on the tool suppliers shelves that is “drill shaped” it’s unbelievable. This is a massive market for the home handyman and consequently everybody and their dog is making them, sadly, most of them won’t last you through a bike build.
There are two very good makes of power tools and they are DeWalt and Makita. Anything else is merely a different level of ****. Don’t waste your money. You want at least 700 watts and if it comes with a hand tightening “quick chuck,” take the **** thing off and replace it with a conventional ½” chuck that is tightened and loosened with a chuck key. “What the ****,” I hear you crying, so I’ll explain. The drill’s purpose is to drill holes. No I won’t apologize for stating the obvious because a drilled hole should be round! How many times have you drilled through a piece of metal to attach rivets or whatever and looked at the hole and it’s vaguely triangular or oval? Remember when our builder friend bought a hub with holes so ****** up a blinded space monkey drugged with acid could have done better? There are a couple of reasons why this happens.
First, dumbassery. There is nothing I can do about that. You’re either a dumbass or you’re not. There, I just saved a third of you from wasting your time on something that is only going to mame, kill, or get your sorry assed divorced.
Next, cheap drills built by jackwagon joe and his dog for the home handyman have poor bearing support on the chuck and consequently the chuck, after a few uses, starts to wander in the housing. This does not happen with DeWalt or Makita stuff. At least I’ve never managed to get them to do it and I try. Ever taken the metal plate out of your head to stop the voices without a proper drill and a securely placed bit? It’s a good way to go end up writing techTips for some stupid ******* online motorcycle magazine or some ****. Another reason is that the hand-tightening chuck has started to loosen and the drill bit is wandering might be a poorly sharpened drill bit, which can cause all sorts of trouble; torn fingers, impalement, pirate eye, and more. We’ll come back to drill bits shortly. First, a photo of Honolulu. Where right now the water is 80 degrees and everybody is walking around in shorts laughing:
We use drills for all sorts of things that we really shouldn’t do, from fitting wire brushes in them to running water pumps to move water out of a flooded basement. These things are why cheapo drills exist. I have probably half a dozen various makes of drills that get used for things other than drilling holes and they all live in a bottom drawer under the bench. My two good Makita drills that I drill perfectly round holes with, they live in the top drawer and are told bedtime stories every night. I smooch them and wish them sweet dreams. Okay, that last bit might be an exaggeration, I only breathe heavily on their handles but they do get looked after a lot better than the cheapo ones and I’ve had them for many years.
Cordless drills:
These things are a bit of a luxury in a bike workshop and we don’t use them a lot but they can be very handy at times. Again, don’t buy cheap ****, if you’re getting one, like a power drill, get at least 14.2 volt but preferably an18 or 24. The really nice thing about a good cordless is battery life. Compared to a cheap one it’s worlds apart. Like Vulcan and Romulus. One cares about co-existing and lives with logic and the other just wants to kick your ***.
And for the ladies, there’s Venus and Mars. One cares but should shut up and the other just wants to kick your ***.
Make sure you have spare batteries – it’s a general rule for any cordless tool – so when you’re using the tool you can be charging the spare battery at the same time.
That’s about it for drills. I’ll summarize with a bit about drill bits. There are a multitude of exotic coated drill bits on the market that seem to be able to drill through anything with the weakest drill you can get your hands on. We’ve all seen the adverts. They are usually gold in color, but it seems we have gotten wise to that so now so the latest are apparently coated in a silvery gray and made of super strong unobtanium alloy that would enable you to walk on the surface of the sun if you coated the soles of your shoes in it.
There is a phrase for these types of products back on my planet, we call it “bollox!” Get yourselves a good set of HSS Drill Bits and good set of Metric ones as well from a reputable engineering tool supply company.
Here’s a tip; the boxes are usually red. Rattle can one of them orange or something, a different color and likewise the bottoms of the drill bits to match the color of the bin they go home in. Trust me that it will save hours of drill sorting fun later. Finally, do some research and find out what drill speed the material your drilling likes to be drilled at! Seriously. The type/thickness/size of hole alter the drilling speed. Get a Zeus Book by begging, borrowing or stealing. Click that link and not only will it make your drilling chores a little easier, but you will save a fortune by not burning out drill bits as well.
Grinders:
We covered bench grinders in Part 1. Nothing to add here so click that link if you forgot. Remember we had them on free-standing mountings so we can move them about, especially outside because nothing clean ever comes off a bench grinder. Well, the same principle applies to hand-held angle grinders. It really isn’t worth spending a lot of money on these, besides you don’t have a lot now because you just spent it on good drills! Again there are so many brands on the market now and they really are very cheap. I have four on the go at any one time.
I’ll explain. One has a grinding wheel on the grinder, one has a cutting wheel on it, one has a wire brush on it, and the last one has a grinding pad for gently grinding discs on it to send to Venus.
These are cheap tools and sharing the workload between them in this way helps them to survive a lot longer and secondly life in the workshop is infinitely more simple when we have tools dedicated to a single use. I don’t believe that given the cost of these things it’s even worth the time searching for different types of discs when you want to go from wire brushing to grinding. It’s much more pleasant to simply pick up the tool with the appropriate disc on it. If you are unable to do this, because you spent your money on a drill, some bits, fancy lighting, wrenches, and socket sets, then one grinder and all the heads you need will be fine.
Saws:
Unless you are going to be building your own frames then I suggest you save space and money and use your hacksaw and vice to do whatever sawing the work you’re doing will entail. But if you are going to be chopping up tubes for frames, we need to talk about the ways to do it.
The three common methods are:
1. The Chop Saw
2. The Band Saw
3. The Jig Saw
1. The Chop Saw: This is very much like a slightly heavy duty version of the carpenters saw used for cutting up wooden studwork on dry walling. Our version has a slightly more powerful motor and usually a fiber-cutting wheel instead of a saw blade, although saw blades that will cut mild steel are now appearing. These things are not my favorite method of cutting up steel. On the plus side they are fast and accurate, but that’s it. On the minus side they are very messy and not only throw steel grindings out the back at a **** of a speed, but the fiber disc degenerates as it’s being used and the mess is incredible. You need to dedicate an area to this tool or the mess will very quickly spread all over your workshop. Remember our enemy is a dirty bench. If you do get one of these blades, I suggest you mount it on a move around trolley of some description and wheel it outside for use.
2. The Band Saw: WARNING WILL ROBINSON! There are very good band saws out there but they are expensive. There are pretty cheap band saws out there that are generally pieces of ****. There are some middle of the road-priced band saws from some of the reputable tool suppliers like Bailey that I’m told are very good. I’m afraid I cant speak from experience about these. You will have to do some research.
What I do know is that whatever make of band saw you get, the first thing you do with it, even before plugging it in, is to change the blade.
All band saws come with cheap and nasty blades that end up twisting and cutting at funny angles. It really is a ride down Misery Street. If you don’t believe me, looky here; scoot to 1:47 for what is probably inevitable if you buy one of those cheap band saws It should be noted that what replaced the one that ended up all over Billy’s floor in pieces was a proper one.
3. The Jig Saw: Jig saws deserve a mention if we are going to be cutting out sheet steel or aluminum to make tanks. These saws don’t often go under a lot of strain as long as we don’t try pushing them through with blunt blades. Change the blade often and buy good ones. There isn’t really a vast amount of **** out there in the jig saw market for some reason. The one I have at the moment cost me about 40 bucks eight years ago and it’s still going strong. I’ve never seen the need to go for a Makita or De Walt version and spend big money on these.
Now that we’ve covered the basics of power tools you will need, it’s time to cast a glance at the more specialized tools that we may need in our future bike building adventures such as compressors, welders and how to build a frame jig.
.
![]() |
“so listen up, punks!” |
Compressors don’t only run spray guns. Yes, as I mentioned in Part 4, we can get air drills, air sanders, air grinders, air chisels, and more to run with compressors. Most air tools don’t need anything like the amount of air that a spray gun requires, and good professional spray guns use in the region of 11 to 14 Cubic Feet per Minute (CFM). I’ll save you all the mathematical working out and tell you the answer. If you are going to spray properly, at a minimum, your compressor needs a 3HP motor.
The size of the tank isn’t that important, although the bigger it is, the less the compressor motor will run between feeding your tool with air. But, as with all things in engineering, there is a pay off. A bigger tank means a bigger piece of equipment which means more space taken up. I alluded to a separate and small lean-to type of building in Part 1 to house the compressor, family and neighbors permitting. If you get a compressor, I would really recommend this course of action and run the air line in through the wall. Coincidentally, a 3HP compressor at the moment is the largest we can get that runs on single phase electricity (AKA 120-volt AC service), which is convenient. If you don’t intend to paint with it then you could go for a smaller 2HP unit and save a few bucks, but you won’t save a massive amount, and you’ll kick yourself later if you change your mind about doing any painting.
My recommendation is to put compressed air in your shop. I don’t do this often, I prefer to lay out the facts and let people choose, but I can’t emphasize how useful compressed air is. From blowing the kid’s – and your own – tires (Yes, I worded that to get a giggle out of ya!), to blowing out carb jets, to painting stuff, it’s one of the most useful tools you can own. Not to mention that once you have one you have access to all the less expensive and more reliable air tools that you’ll be able to use.
Now on to welders. Good grief! This is really a subject that I could do a whole article about. I’m going to be quite brief because if you can weld already, you don’t need me to confuse things for you and if you can’t, you won’t learn how to from an article on the internet. You’ll have to take a course or at the very least team up with a buddy who has all the gear and get him/her to teach you.
There are four major welding disciplines in use today, two minor ones, and a couple of high-tech laser based systems in use by NASA, the aviation industry and I believe the Volkswagen Group (Volkswagen, Audi, Bentley, Bugatti, Lamborghini, SEAT, Skoda, and Scania).
We are really only interested in the major four. We’ll leave the high tech stuff to the aliens and their Luftewaffe buddies in the USA.
It would be downright criminal of me if I didn’t warn you that if you can’t weld, don’t attempt it without some instruction. I have literally seen bike frames come apart at the seams and the consequences of that happening are never very pleasant. Please DO NOT take chances, YOU MIGHT DIE!
Now let us briefly look at the disciplines anyway. This way if you know what they are, it should help you decide whether or not you want to learn them.
![]() |
tig welding for dummies! |
1. Oxy-Acetylene (OA) welding (commonly called gas welding). I’m sure you’ve all seen examples of this done. There are two large gas bottles; one is black (oxygen) and one is red (acetylene). These two gasses get mixed at the nozzle of the welding torch and are lit to produce a very hot and small blue flame that will melt steel very quickly. The idea is to melt the two pieces of steel together in a small continuous pool and fill in between with a filler rod made of steel. It’s a very skillful process and hard to do without a lot of practice and instruction. OA used to be the way almost everything automotive was welded. It’s very effective because the welder has to pay attention to every inch of weld he’s welding, therefore a bad weld is actually quite difficult to achieve. It’s drawback on sheet metal is that it’s a long process relative to the other disciplines and that can cause distortion on flat panels. That’s not a lot of use to us in bike building.
2. Arc Welding. This is the old type of industrial process used on everything from pipelines running through Alaska to truck chassis. It’s fast and cheap and it’s relatively easy to learn. The operator has an electrode (AKA the welding rod) attached to an insulated grip, and the piece to be welded is attached to an earth lead between it and the welding machine. To weld, the operative touches or “arcs” the electrode to the workpiece and the subsequent short circuit melts the metal. The happy worker bee fills in between the metal pieces with his electrode filler rod. As I say, the plus to arc welding is that it’s cheap, quick and easy to learn. It’s downside is that because of the amperages involved, arc welding thin gauge metal can be next to impossible without the absolute state of the art welding machine and a very good welder, which means it’s only really useful for heavy stuff. Again, not a great deal of use for bike building.
3. Metal Inert Gas (MIG) Welding. This is a welding process that was originally developed back in the 1940’s for welding aluminum and other non-ferrous metals. MIG welding is a semi-automatic process in which a wire connected to a source of direct current acts as an electrode (much like the Arc Welding process) and joins two pieces of metal as it is continuously passed through a welding gun. A flow of an inert gas (usually Argon) is also passed through the welding gun at the same time as the wire electrode. This inert gas acts as a shield, keeping airborne contaminants away from the weld zone. In it’s favour MIG has a lot going for it; it’s quite easy for the beginner to learn, it’s a fast procedure which makes it suitable for sheet metal, and it’s in common usage and therefore relatively cheap. Both the cost of the welding machines themselves and the consumables are what I consider affordable to the garage builder. The drawback is that it is very easy for the beginner to think that he/she has a good weld but in actual fact the weld doesn’t have enough penetration. It’s very easy to do “pretty” welds with a MIG, but pretty welds are not necessarily good welds. I would advise getting some instruction!
4. Tungsten Inert Gas (TIG) Welding. TIG welding is an arc welding process that uses a non-consumable tungsten electrode to produce the weld. The weld area is protected from atmospheric contamination by a shielding gas, usually an inert gas such as Argon, and a filler metal is normally used, though some welds, known as autogenous welds, do not require it. A constant-current welding power supply produces energy which is conducted across the arc through a column of highly ionized gas and metal vapors known as a plasma. This is the popular process used in bike building today. See photo on the left of the sort of weld it is possible to achieve using TIG. The process is actually a cross between gas welding and MIG, in so much as the welder needs the skills of the gas welder in technique which is very similar, but the welding process is pretty close to what happens in MIG welding, where the electrode is manually introduced instead of fed automatically from a spool in the machine. Nearly all the bike builders and factories today TIG weld their frames. The plus side of TIG is that the welds are nearly always very good to perfect, dependent on the skill of the operator, for the same reasons as gas welding. The downside is the equipment is expensive, it is also arguably the most difficult welding technique to master and therefore, GET SOME INSTRUCTION!
The next two items we are going to look at putting in our workshop are a tube bender and a frame jig. If you want to build your own frames, or even change up any original donor frame, these two really are a must. So don’t be a dumbass and start cutting up the frame of your bike to put in a fancy single down tube without a frame jig. Don’t even hardtail your original frame without one. Seriously. You’ll just build some unrideable piece of ****.
We’ll start with the bender.
![]() |
jd squared – model 3 | tube bender |
1. Tube bender. To bend structural tube, which is what bike frames are made of, we need a decent bender. There are a few on the market. One is a ratchet bender called the JD Squared, Model 3. This is a very good bender for the small operative or the home builder. I have owned and used one in the past and it works very well. I believe it to be reasonably priced ($295), and if your budget would allow it then I would definitely recommend one of these as an option. They are robust and relatively straightforward to operate, but when bending something like 1.25″ CFS 3 (DOM seamless) for example, it is necessary to use a long handle and a second pair of eyes to watch the degree wheel and make sure you don’t bend too many degrees! You can keep pulling and checking and pulling and checking but besides being time consuming, the one thing that benders will not do if you go to far is bend it back! It should be noted that a hydraulic adapter be fitted to the Model 3, which negates the long handle and turns it back into a one man operation but, as with all things, this accessory has a price ($95).
Another bender is the Pro 3 from Pro Tools. This type of bender in my humble opinion is far easier to use, and we are less likely to go past our desired bend point because we are looking directly at the gauge. Although it has to be said that it costs 40% more and I like the JD Squared Model 3. These two are good examples of what’s out there on the market today.
One thing to bare in mind if you’re thinking about buying a bender is to determine if the machine itself is merely a paperweight without die sets. You can see in the video above that dies are needed and there are costs involved in buying them. If you’re thinking of doing different types of frames, instead of repeating the same one over and over, or simply building one, then you will need at least 7/8″, 1″ and 1.25″ die sets and more from 150 to 300 bucks a pop. You can see how it can turn into a big investment. Know what tubing you’re using, build with that, and go from there. Let a new client’s deposit for some other diameter pay for your new die set.
![]() |
home made bender 1 |
![]() |
home made bender 2 |
Look at these “Bite My Shiny Metal ***” pics above. You’ll see that in principle it is pretty much the same as the Pro 3 setup, but more compact, even as the idea is the same. See, an hydraulic ram pushes the die set around and bends the tube to the required degree. I mention the “Bite My Shiny Metal ***” bender above because we are on a budget, and this is a home-made option. You can Google “home made benders” and maybe you’ll find something cool and affordable.
The cost in total when I built this bender was under 50 bucks plus the die set. In fact I saved at least the cost of one die set if not two by building my own bender. If there is enough interest I will make the drawings available through bikerMetric at a future date and write an how to article on how to build one. It really isn’t difficult, with the tooling we have talked about having in our shop above in place I would label the task as an “easy to medium” level in difficulty.
[EDITOR’S NOTE: Um, **** yeah, dude! And Matt Groening’s attorneys just emailed me. He wants money if we mention “bender” one more time. If we do, we have to print “Matt Groening” three times.]
You will see from looking at the two popular options above that bending tube is a serious and not a very cheap business. Although having said that, you will find that once you have a bender in your shop you will develop a whole new network of ‘friends’ who want this or that bending, in short it’s not beyond the realms of possibility that it could pay for itself before long.
2. Frame jig. This is a controversial subject. Everyone has an opinion on what is required of a frame jig. Let’s start by getting things in perspective. There are two types frame jigs and both of them have only one purpose; to hold pieces of tubing firmly relative to each other that enable us to weld them together precisely. The first type of frame jig, which every motorcycle builder must have, is very basic and has no adjustability in it since it is designed to hold a certain dimension of “part” (say a 1979 Yamaha XS650) and is only used time after time for builds of one model/size frame only (like building multiple 1979 Yamaha XS650s). These are known as “production jigs” and are used in factories which turn out multiple frames that are exactly as the one preceding the other day after day.
Excuse me. I had to yawn.
For a “production jig,” all one has to do is clamp and reclamp… [EDITOR’S NOTE: Dammit, Matt, you said “bender.” Clamps has nothing to do with our agreement!]… the precut/bent pieces of tube in and weld them together. These jigs are a fast and efficient way of holding pieces of tube relative to each other to build a frame.
The second type of frame jig i call an “adjustment jig,” because it has adjustment abilities dialed in to it at every level; including rake, wheelbase, ground clearance and more. They are used by factories for research and development and prototyping. Chances are the first frame on any production model out there was pulled off one of these jigs, with measurements duly taken on the fitments and clamps from production jigs then made up to match it’s configuration to go into production. The re-configured jig is then set, possibly for the next concept based off it’s original design.
The reality is we need an “adjustment jig.” It’s very unlikely that the first frame idea we come up with, however killer it’s design, is going to satisfy us forever. When we want to build another one, we are either delving back into our pockets to build another jig or to fund modifying the one we have, which isn’t what we want any more because we might want different frame parameters. If you want to go to the lengths of building your own frame, it just doesn’t make sense financially or other wise to build a production jig. Take a look at the frame jig photo below:
![]() |
adjustment jig – front |
The jig above is on a bench where a guy or gal is able to get all around it to weld and curse that the sandwich hasn’t arrived and there is no beer. It’s a pretty common set up made basically of a thick steel bed with the jig fixtures either welded to it or bolted down through pre-drilled and possibly tapped holes. The neck is adjustable for both rake and height. It’s a neat and tidy set up and should work well for all garage builders. Considering that for us, space is at a premium, we would need this to be easily wheeled or moved out of the way when it’s not is use.
![]() |
adjustment jig – side |
The photo above, taken in a naughty gynecologist’s office, you see a jig that is movable, fully adjustable for all aspects of the frame, and can be rotated to facilitate welding the lower rails and underneath without having to take the frame out of the jig very often. In fact, with this jig we can weld almost completely around every frame tube and when we do take it out, it’s only to finish welding the last hard-to-get-to areas. The only reason to put the frame back in the jig after that is to check and see that no misalignment has occurred in the final stages.
That is a frame jig’s most important aspect; to keep frames straight. Without one, you’re a pretender and again, building a bike that will be unsafe and unrideable. You’ll kill yourself or somebody else that way.
As you can see a frame jig is not a half-assed affair and needs to be sturdy and able to hold various fitments and clamp the frame tubes in place whist they are welded together.
The jig in these pics are known as “Mr. Stiffy” (a very naughty gynecologist) and like the bender, if there is enough interest shown I will make the drawings to build this jig available through bikerMetric at some time in the future and do an article on how to build one.
The last item to mention in this two thousand and twelve-piece article is an adjustable bike stand or lift. On my planet there are only two types:
![]() |
rich people slumming on bikerMetric… |
![]() |
you. |
See the pics above for what they look like. Keeping in mind our constant need to be wary of space (or the lack of it) and money. I’d suggest the first example might be too large for us. Yeah, it could work in the space we have available but it takes up too much room in my opinion the cost could be better spent elsewhere, such as beer and ********, or an air compressor and proper saws. Then there is what to do with it when not in use. It’s a big item even when static.
So what to do? We really do need something to allow our pride and joys to progress and develop. It’s great to have the bike up off the floor at a level where we are not constantly on our knees or bending over and putting strain on our backs, knees and elbows. Yes, we could build it up on a bench or table placed in the center, and that would certainly get rid of the bending and knee problems, but what do we do when it’s finished? The bike is not so easy to get down when complete as it is easy to get up there in pieces. Have a look the last photo above. These things really are a godsend. Get one. End of discussion.
The last piece of equipment I will mention is a fridge! Yep, a fridge.
Remember, your brew kit for tea/coffee/cocoa whatever, and kettle will all be neatly occupying a small corner of a bench somewhere ready for use periodically. You need somewhere to put your milk. I don’t care if you take yours black, I don’t, and if I decide to pay you a visit one day you’ll be very embarrassed to not be able to offer me my coffee how I like it after I’ve gone to all this trouble to tell you all these things and more. A fridge is also a jolly good place to store your beer for other peoples visits, like Trent’s, and a bottle of wine for visits from Frank and hot babes you want to impress.
If you want an engineering reason for a little refrigerator, store your Loctites, graphite greases and CopperLube in there as well. Oh, and Super Glue. Refrigeration makes it harder to get out that way but it lasts longer without solidifying.
I’m finishing the tools saga here and now. It’s time to move on and actually put this fantastically well equipped super space to use and build a bike.
If there is anything you guys think I’ve missed or haven’t covered in enough depth, feel free to **** off contact me through bikerMetric and ask away. Please remember that the only “stupid question” is the one that you were either too afraid or too embarrassed to ask! Nobody knows everything, and even seemingly simple questions make us think.
Next time we will look at frames:
Do we buy one or do we make one? That’s the dilemma we’ll be discussing. There are pros and cons to both routes as we will see.
Stay tuned and watch this space. Oh, and two sugars in my coffee.
And to complete our legal agreement, I must end this segment with “matt groening.”
Great information and good read. I want to take the skills I have already developed and push myself to a new level of craftsmanship. Hoping to build my first scratch bike this winter after having restored my 1985 Harley FXR. Thinking about a Triumph chopper.
The fridge is also a good place to put bearings so they pop in easier on the warm bike!
Thanks for the great article mate, it was so easy to read I didnt notice how ****** long it was! Id really appreciate the plans for “Mr Spiffy” if you get the chance. Keep up the good work
very, very nice page,,,
Enjoyed your article man. I would like to see someball park pricing for the items mentioned so that those that are new to this would have an idea of how much they would have to come out of pocket. Just a thought.
great stuff here! was very interested in the crankshaft mod. would like to learn all these skills to make some amazing custom bikes of my own. Motorcycles is my life!
Awesome page…looots of helpful tips…love the “beer hunter” poster :D
Remember:Always the rubber side down!
Learned a lot and some new beer brands
its good